Walter Kraus Produktions- und Organisationsmanagement in Presseartikeln und Podcast
Podcast
Was können Sparkassen und Banken von Produktionsunternehmen lernen?
Prof. Dr. Jürgen Weimann im Gespräch mit Walter Kraus über Prozesse und ihre Bedeutung
Everyone Counts – Transformation für Banken und Sparkassen
FOLGE 127. 08. Januar 2024
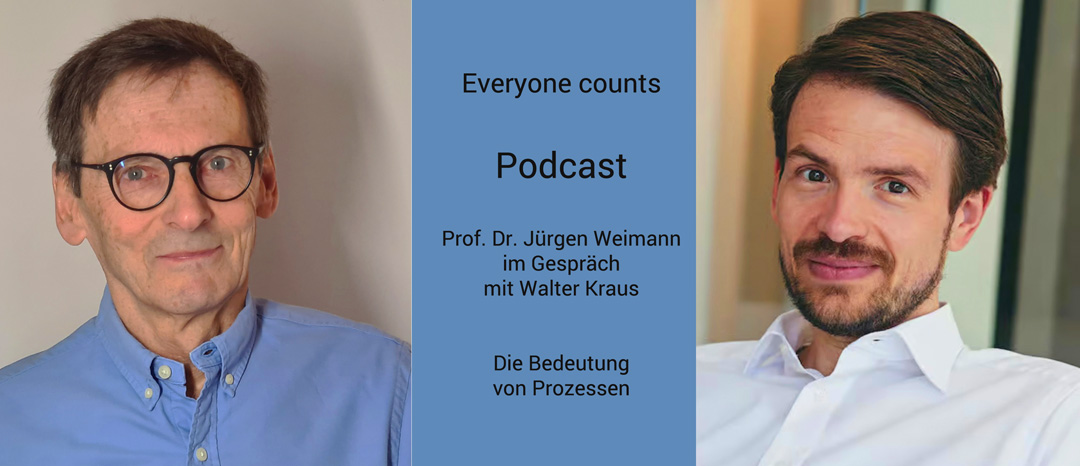
Determinierte Prozesse sind unverzichtbar. Sie synchronisieren die Vorgänge an verschiedenen Standorten, sichern Produktqualität, Wiederholgenauigkeit und machen Ergebnisse vorhersagbar.
Geschäftsprozesse in Unternehmen können aber auch wie ein Korsett wirken. Nämlich dann, wenn sie ein flexibles Reagieren auf die Dynamik der Märkte erschweren oder verhindern. Dieses Dilemma erfordert es, in bestimmten Phasen oder Situationen Prozesse „floaten“ zu lassen und die Experten am Ort des Problems pragmatisch entscheiden zu lassen.
Presse
Ohne Umsetzung kein Beratungserfolg
Die Rolle der Beratungshaltung für die Umsetzungsmotivation
Erschienen in OrganisationsEntwicklung. Zeitschrift für Unternehmensentwicklung und change management.
ausgabe 02/24, Seite 109 ff.
Fehlt für Veränderungen die Umsetzungsmotivation bei Betroffenen und/oder Entscheider:innen macht die Vergabe eines Beratungsauftrags wenig Sinn. Das kostet Zeit, Geld und führt zu Frust auf beiden Seiten.
Erstveröffentlichung in der OrganisationsEntwicklung 02/24, www.zoe-online.org.
Leseprobe mit freundlicher Genehmigung © Handelsblatt Media Group.
VDI München: Potenziale einer guten Fehlerkultur
Vortrag von Walter Kraus für den VDI
Verein Deutscher Ingenieure, Arbeitskreis Unternehmer und Führungskräfte
Erschienen in Technik in Bayern, Nachrichten aus Technik, Naturwissenschaften und Wirtschaft.
Ausgabe 01/2024, Seite 31.
Warum tragen wir alle Glaubenssätze zum Thema „Fehler“ in uns und woher kommen diese? Im Münchner VDI Arbeitskreis Unternehmer und Führungskräfte ging Referent Walter Kraus ausführlich auf diese komplexe Fragestellung ein.
Die Supply Chain (Lieferkette) am Beispiel eines KMU
PRESSE Erschienen in Technik in Bayern, Nachrichten aus Technik, Naturwissenschaften und Wirtschaft.
Ausgabe 03/2017. Seite 16 bis 18.
Warum ist die Entwicklung und Umsetzung einer funktionierende Supply Chain Strategie so wichtig? Welche Faktoren sind zu berücksichtigen? Am Beispiel eines mittelständischen Unternehmens aus dem Hightech-Bereich werden die Themen „Supply Chain“ bzw. „Supply Chain Management“ und ihre Herausforderungen beschrieben.
Die Supply Chain hat eine lange Tradition
Bereits im vorindustriellen Zeitalter, d. h. in Zeiten von Handwerk und Zünften, war eine funktionierende Versorgungskette Voraussetzung dafür, dass der Hersteller seinen Kunden bedienen konnte und dieser das von ihm gewünschte Produkt erhielt….
Kein Unternehmen ohne funktionierende Supply Chain
Kein Unternehmen kann ohne strategische Überlegungen zur Supply Chain erfolgreich auf dem Markt agieren. Bereits vor der Gründung müssen 3 Fragen beantwortet werden:
- Welches Produkt will ich anbieten bzw. an wen verkaufen? → Kunde
- Welche Wertschöpfung (an diesem Produkt) erzeuge ich innerhalb meines Unternehmens?
- Was brauche ich für diese Wertschöpfung von außen? → Lieferant
Krise für den Mittelstand?
Erschienen in der Zeitschrift Optik & Photonik.
Ausgabe 01. April 2009. Seite 8 bis 9.
Dr. Wilhelm Kaenders im Gespräch – Mitgründer der Firma TOPTICA Photonics AG
TOPTICA wurde am 17. Februar 2009 elf Jahre alt. Wenn Sie zurückblicken, was waren Ihre wichtigsten Erfolgsfaktoren bei der Gründung?
Kaenders: Die Firma ist aus dem Windschatten der Technolas/TuiLaser gestartet und hat anfänglich von dem Förderprogramm des Bundes (Programm Laser 2000) profitiert…. Unser Geschäftsansatz ist ambitioniert, aber solide und langfristig angelegt, so dass sich Technologie entwickeln kann. Das Feld der Laserkühlung und Präzisionsspektroskopie von Atomen und Ionen, in das unsere ersten Produkte zielten, wurde 1989, 1997, 2001 und 2005 mit Physik-Nobelpreisen ausgezeichnet und hat einen enormen Aufschwung erfahren, in dessen Verlauf wir unsere Geräte als Standard etablieren konnten.
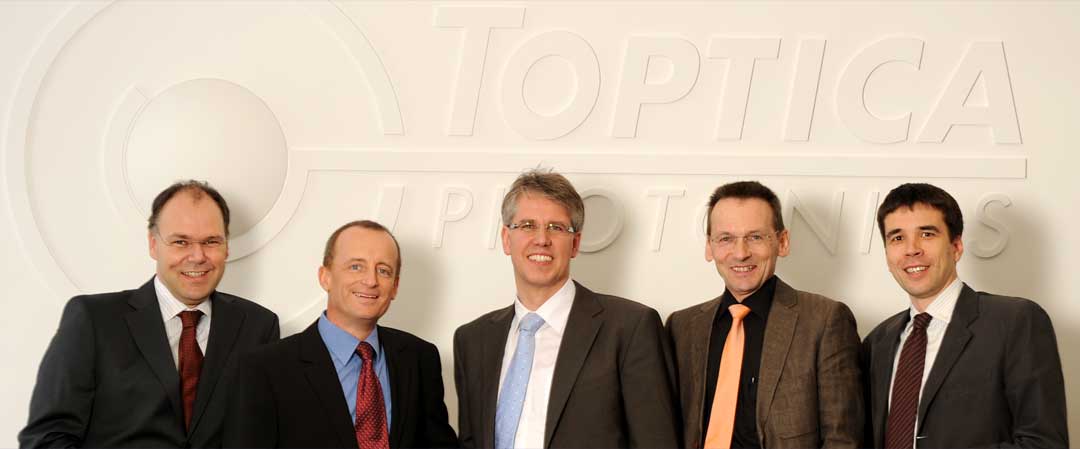
Lasertechnik für Goldschmiede – Interview mit Walter Kraus
Erschienen in der Süddeutschen Zeitung.
Ausgabe 215 vom 18. September 1996.
Mit „echtem high tech“, so Walter Kraus (damaliger Bereichsleiter für den Geschäftsbereich Serienprodukte bei Baasel), hätten sich die Goldschmiedehandwerker noch so gut wie gar nicht befasst. Aus diesem Grunde wollte der Hersteller von Lasern und Lasersystemen dieser Berufsgruppe die Berührungsängste nehmen und zeigen, in welchen Bereichen das moderne System von Baasel zur Gold- und Silberbearbeitung einsetzbar ist.
Der Laser macht Dampf – Laser-CVD für die Leiterplattenindustrie
Erschienen in Laser. Entwicklung und industrielle Anwendung.
Ausgabe 3. August 1990. Seite 158 bis 160.
Die Reparatur von Mehrschichtkeramikträgern in der Leiterplattenindustrie ist oft recht schwierig. Durch Prozessfehler oder kleine Verunreinigungen entstehen Unterbrechungen auf den winzigen Leiterbahnen aus Gold. Mit Hilfe eines Laser-CVD-Verfahrens können diese Bauteile instand gesetzt werden …
CVD steht für Chemical Vapor Deposition, also chemische Dampfabscheidung. Dabei wird eine Kammer bis zu einem bestimmten Druck evakuiert und anschliessend mit einer gasförmigen Verbindung wieder gefüllt. Diese metallorganische Verbindung enthält – zunächst molekular gebunden – ein Metallatom wie z. B. Gold, Palladium, etc., welches bei Einwirkung von grosser Hitze freigesetzt wird. Es entsteht sozusagen Metalldampf.